How Hot Laminating Machine Creates PVC Tarpaulin
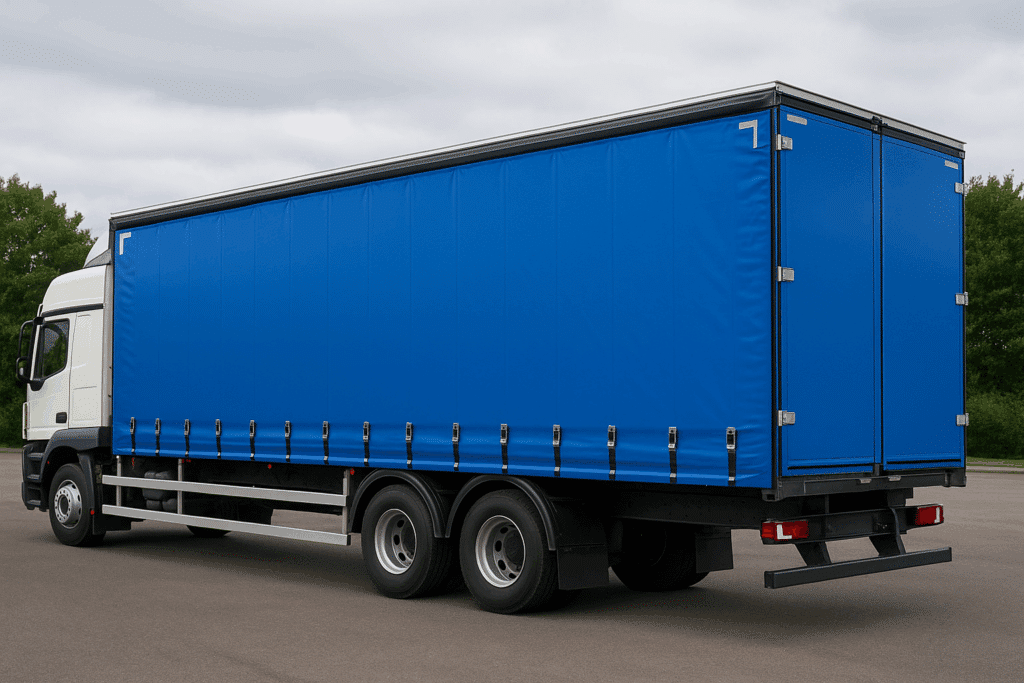
Introduction to PVC Tarpaulin Manufacturing
PVC tarpaulin has become an essential material across numerous industries due to its waterproof properties, durability, and versatility. Behind every high-quality tarpaulin is a sophisticated manufacturing process, with hot lamination standing as the premium production method. This advanced technique creates superior products that withstand harsh environments and heavy-duty applications.
The Professional Hot Laminating Machine
Hot laminating machines represent the PRO version of standard cold lamination equipment, delivering exceptional results through a more complex and thorough manufacturing process. These industrial machines require significant investment but produce tarpaulins with superior technical specifications and longevity.
Key Components and Features
The hot laminating machine contains several sophisticated components:
- High-temperature heating systems capable of reaching and maintaining precise temperatures throughout the production cycle
- Advanced pressure application mechanisms that apply uniform force across the entire width of materials
- Complex embossing rollers designed to create specialized surface textures and patterns
- Multi-stage surface treatment systems that prepare materials for optimal adhesion
- Precision control systems monitoring temperature, pressure, and speed variables
- Extended production line length accommodating the longer processing time required
These machines typically occupy substantial factory floor space due to their comprehensive processing capabilities, with production lines often extending 30-50 meters in length.
The Three-Layer Manufacturing Process Explained
Hot lamination creates PVC tarpaulin through a precise sequence of operations:
Stage 1: Fabric Preparation and Initial Coating
The process begins with dense, high-quality base fabric—typically polyester or similar materials with tight weave patterns. Unlike fabrics used in cold lamination, these materials have minimal gaps between threads. The machine applies a precise layer of liquid PVC directly to this fabric, creating a foundation layer that penetrates partially into the weave structure.
Stage 2: Primary Lamination
Once the initial coating adheres to the fabric, the machine applies the PVC film layer. This isn’t simply placed on top—the equipment uses carefully calibrated heat and pressure to begin the bonding process. At this stage, the three distinct layers (fabric, PVC coating, and PVC film) are aligned and initially joined.
Stage 3: Heat Treatment and Final Bonding
The partially-bonded material then travels through an extensive heating oven system. Inside, temperatures are precisely controlled to activate chemical bonding agents and create molecular cross-linking between layers. This critical stage transforms the separate components into a unified material with significantly enhanced properties compared to the individual layers.
Stage 4: Surface Treatments and Finishing
After primary bonding, the hot laminating machine can apply additional treatments:
- Acrylic coatings for self-cleaning properties
- UV-resistant compounds to prevent sun damage
- Fungicide treatments for mold resistance
- Fire-retardant chemicals for safety applications
- Anti-static treatments for specialized uses
The Hidden Complexity Behind Quality Production
While the process may sound straightforward, creating high-quality PVC tarpaulin through hot lamination requires extensive knowledge and expertise. The reality involves complex material science and precision manufacturing that takes years to master.
Expert Knowledge Requirements
Production managers must possess comprehensive understanding of:
- PVC polymer chemistry and behavior under varying temperatures
- Specific additive formulations and their interactions
- How different fabric substrates respond to coating processes
- Precise temperature and pressure requirements for optimal bonding
- Chemical compatibility between layers and treatments
Challenges of Production
The longer and more complex process of hot lamination creates significant challenges:
- Even minor mistakes can result in products with incorrect GSM (grams per square meter)
- Insufficient bonding between layers can cause premature delamination
- Extended production runs increase difficulty for operators who must maintain precise conditions
- Material variations require constant adjustments to maintain quality
- Surface treatment timing must be perfectly synchronized with bonding stages
One production expert noted: “What looks simple on paper becomes incredibly complex when you’re managing a 40-meter production line where temperatures, pressures, and chemical interactions must all be precisely controlled simultaneously.”
Technical Advantages of Hot Laminated Products
The hot lamination process creates tarpaulins with several superior characteristics:
- Enhanced air tightness due to the high-pressure film application process
- Superior bonding strength between layers, preventing delamination
- Increased tensile strength compared to cold-laminated products
- Better resistance to UV degradation through improved material integration
- Extended product lifespan of typically 2-5 years longer than alternatives
- Improved chemical resistance from the thorough heat-treatment process
The Importance of Experienced Manufacturers
When sourcing PVC tarpaulin, the manufacturer’s experience directly impacts product quality and consistency. You want to look for someone with years of experience in the industry to provide consistent quality and stable products that don’t cut corners.
Experienced manufacturers maintain supportive supply chains with materials made to exact specifications. They understand the critical balance between cost efficiency and quality assurance, ensuring that each production run meets stringent standards.
SKP Material stands out with extensive experience in the field. Their production team brings decades of combined expertise to each tarpaulin manufactured, resulting in products with reliable performance characteristics that meet or exceed industry standards. Their knowledge of PVC formulations and processing techniques ensures optimal results across diverse applications.
Applications Across Industries
Hot laminated PVC tarpaulins excel in demanding environments:
Marine Applications
The superior air tightness and waterproofing make these materials ideal for boat covers, dock shelters, and marine equipment protection where constant exposure to moisture is unavoidable.
Aquaculture Solutions
Fish farms and aquaculture operations rely on these tarpaulins for water containment, equipment protection, and specialized holding tanks due to their exceptional durability and non-toxic properties.
Transportation and Logistics Applications
The transportation industry heavily relies on hot laminated PVC tarpaulins for their exceptional durability in constant-motion environments:
Truck Tarpaulins and Curtains
Hot laminated PVC is the preferred material for truck side curtains due to its ability to withstand:
- Continuous wind pressure at highway speeds
- Frequent folding and unfolding during loading operations
- Exposure to road debris and environmental pollutants
- Constant UV radiation during long-haul transport
Truck curtains manufactured from hot laminated materials maintain their appearance longer with less sagging and degradation, offering superior load protection and improved fuel efficiency through better aerodynamics.
Asphalt Tarps for Rigid Trucks
Specialized asphalt tarps require exceptional heat resistance and tensile strength. Hot laminated PVC tarpaulins used in this application feature:
- Enhanced heat-resistant additives that prevent melting or deformation
- Reinforced edges that resist tearing under heavy use
- Superior resistance to petroleum-based chemicals found in asphalt
- Increased puncture resistance from aggregate materials
Highbed Trailer and Standard Trailer Covers
Trailer operations present unique challenges for covering materials:
- Oversized loads requiring custom dimensions
- Extended exposure to highway conditions and weather extremes
- Frequent securing and unsecuring with tie-downs
- Complex load shapes requiring conformable yet strong materials
Hot laminated PVC outperforms alternatives in these applications due to its ideal balance of strength and flexibility, providing reliable load protection while maintaining ease of handling for operators.
Outdoor Structures
From commercial tents to event structures, the enhanced strength and weather resistance provide reliable performance in unpredictable outdoor conditions.
Industrial Covers
Manufacturing facilities use these materials for equipment protection, containment solutions, and specialized covers where strength and longevity are essential.
Why “Semi-Coating Machine” Is Also Accurate
The hot laminating machine is sometimes called a “semi-coating machine” because it combines two manufacturing approaches:
- Traditional coating – applying liquid PVC directly to fabric
- Film lamination – adding pre-manufactured PVC film
This hybrid approach delivers the advantages of both methods while minimizing their individual limitations, resulting in a superior end product.
Conclusion: The Value of Advanced Manufacturing
The hot laminating machine represents a significant advancement in PVC tarpaulin production technology. While the process requires more time, energy, and specialized equipment than alternative methods, the resulting products offer substantially improved performance characteristics and longevity. For applications where reliability and durability are paramount, hot laminated tarpaulins provide exceptional value despite their higher initial cost.
Links: Our PVC Tarpaulin Learn More